SMIC Begins Volume Production of 14 nm FinFET Chips: China’s First FinFET Line
by Anton Shilov on November 14, 2019 1:00 PM EST- Posted in
- Semiconductors
- 14nm
- FinFET
- SMIC
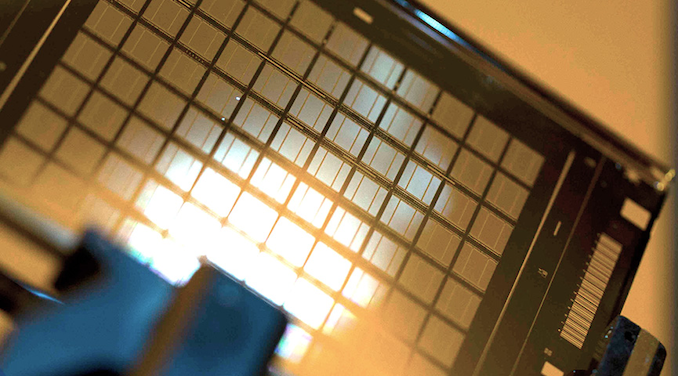
SMIC has started volume production of chips using its 14 nm FinFET manufacturing technology. The largest contract maker of semiconductors in China is the first company in the country to join the FinFET club, as only a handful of companies have managed to develop fabrication processes that rely on such transistors. SMIC’s FinFET line is considerably smaller than those of other foundries, yet the fact that the company is using it is already a big deal for China.
SMIC’s previous-generation manufacturing technology is 28 nm, so the 14 nm process tangibly increases transistor density, boosts performance, and lowers power consumption, which naturally enables the company to produce more complex and expensive chips that were otherwise outsourced to its larger rivals. At present, SMIC ramps up production using its 14 nm process technology at one of its 300-mm fabs, so initial volumes are not high. Meanwhile, SMIC’s plans include building up a new 300-mm production line for 14 nm and thinner process technologies with a monthly capacity of 35,000 wafer starts per month. Construction of the fab was completed earlier this year and the company is currently installing production equipment.
In addition to ramp of its 1st Generation FinFET platform, SMIC’s development of its 12 nm process is well underway and there are customers who plan to use the technology. Furthermore, the company is developing more advanced processes, including those that will require extreme ultraviolet lithography (EUVL) tools, that will be used next decade. In fact, the company has even acquired an EUV step-and-scan system from ASML, but it has not been installed so far.
Being relatively small foundry, SMIC is gradually closing the gap between itself and larger rivals when it comes to technology development. Meanwhile, because each new process costs more in terms of R&D, companies need to increase their production volumes to make development financially viable. Therefore, it is crucial for SMIC (and other foundries) to procure advanced production equipment on a timely manner and increase their manufacturing volumes for long-term success.
Dr. Zhao Haijun and Dr. Liang Mong Song, SMIC's co-CEOs said in their joint statement:
"Over the past two years, we have not only narrowed the advanced technology gap, but also expanded comprehensive mature node technology platforms. We have confidence that with the wave of 5G applications, we will enter a new stage of development.
[…]
FinFET technology development continues to push forward: the first generation of FinFET has already successfully begun mass production and will begin to contribute revenue in the fourth quarter; meanwhile, the development of second generation of FinFET is steady, and customer engagement is smooth. We believe that SMIC will benefit from the extensive business opportunities brought by the upcoming 5G product migration, and we will exit this period of transition and re-enter growth."
Related Reading:
- SMIC: 14nm FinFET in Risk Production; China's First FinFET Line To Contribute Revenue by Late 2019
- SMIC To Start 14nm Mass Production in H1 2019
- GlobalFoundries and Chinese Authorities Reconsider Plans
- Intel to Expand Production Capacities at Multiple Fabs
Source: SMIC
15 Comments
View All Comments
Diogene7 - Thursday, November 14, 2019 - link
I am not sure, but I think that Globalfoundries stop at 12nm : it means that SMIC is getting closer to be on-par with Globalfoundries in terms of node...ksec - Thursday, November 14, 2019 - link
The difference is GF are shipping them with decent yield, while SMIC has a track record of Press Release with no yield.brantron - Thursday, November 14, 2019 - link
GF has a 7nm process, but due to the cost of mass production (or so they say), what they were working on is being applied to a lower cost DUV process. It sounds like a half-node on steroids.https://www.anandtech.com/show/14905/globalfoundri...
And then there's the cross-licensing deal with TSMC. Whatever in the world they're up to, they aren't just calling it quits at the existing 12nm.
https://www.anandtech.com/show/15038/globalfoundri...
yannigr2 - Saturday, November 16, 2019 - link
@brantronThey tried to sue TSMC, then TSMC reacted. They probably signed whatever TSMC's lawyers gave them to sign.
TristanSDX - Thursday, November 14, 2019 - link
lol, chinese are now equal to Intel, something unbelievable few years ago. US is loosing technological lead.webdoctors - Thursday, November 14, 2019 - link
arent these just marketing numbers? I thought Intel 14nm =Samsung 7nm=TSMC 12m? Maybe there should be a mapping table somewhere.brantron - Thursday, November 14, 2019 - link
Transistor density, very generalized, doesn't mention all the variations of each node:https://www.techcenturion.com/7nm-10nm-14nm-fabric...
More detailed, but slightly out of date, and current info may not be available yet:
https://semiwiki.com/semiconductor-manufacturers/i...
sseemaku - Thursday, November 14, 2019 - link
Whey didn't any European company develop such fabs. They couldn't do it or they didn't wanted to? Wondering if the Chinese have surpassed Europe in tech!Death666Angel - Thursday, November 14, 2019 - link
Europeans see themselves as buddies with the US, so they see no need to have their own technological thing going because of mistrust. AMD has a large fab in Dresden, does Infineon operate fabs? Most fabs on the world were a loss business apart from Intel (we don't know) and TSMC. Even Samsung fabs aren't making a profit last I read (not talking DRAM or NAND).And "tech" is a whole lot more than what is convered in this article.
wr3zzz - Thursday, November 14, 2019 - link
Semi fab industry evolve either mostly top down (Japan, Korea, China) or bottom up (US, Japan also, Europe, Taiwan). The top down model did not end well. The old Japanese semi national champions have all gone bust. Korean almost did and could be again as the Chinese are copying what they did to the Japanese. Bottom up companies cater to demands. The European industrial base first lost PC and then smartphone. Now like Japan its semi fabs cater to industrial applications, sticky but not node demanding.